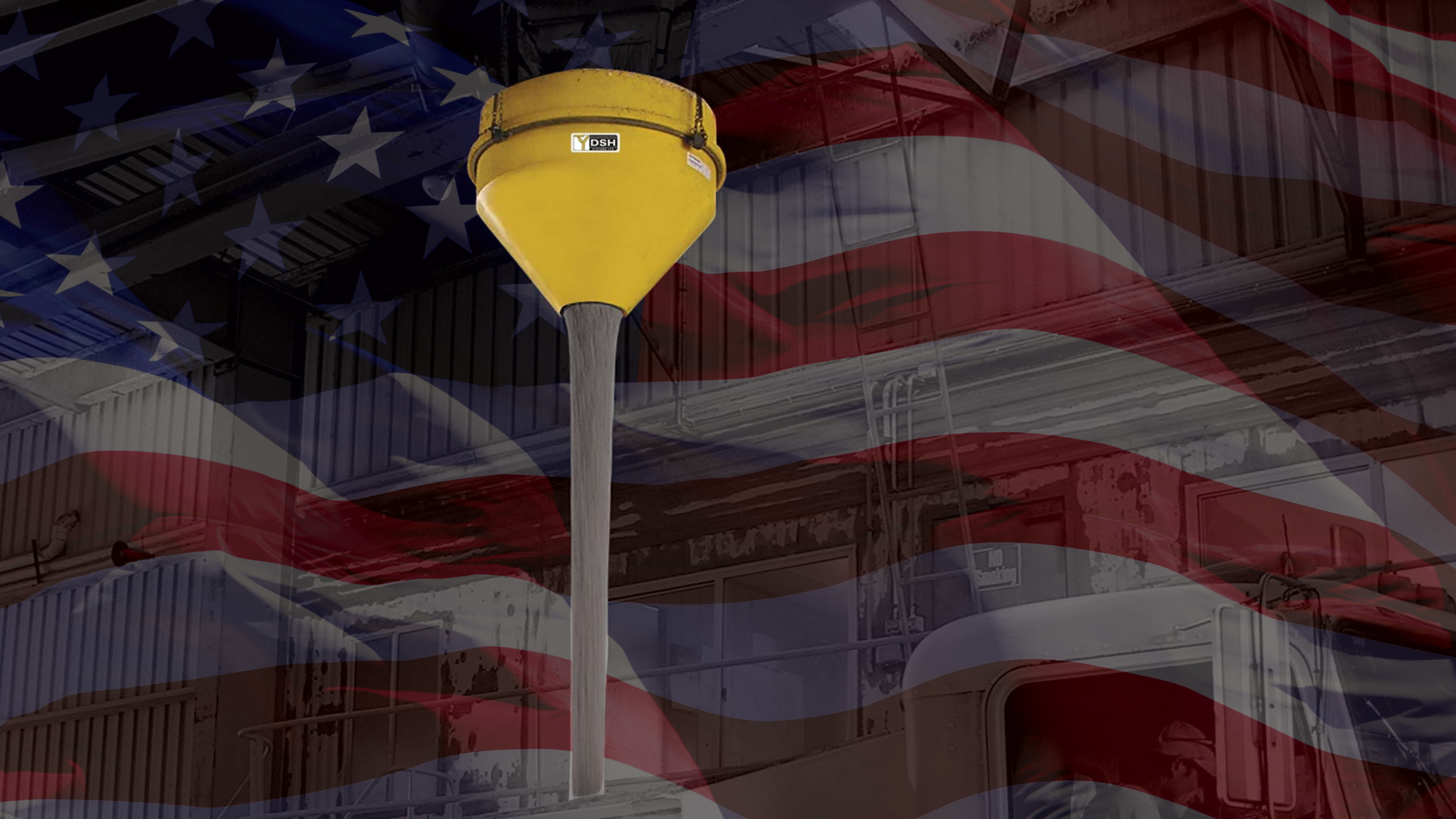
Your Cost Effective, Simple Dust Control
Solution for Near Dust-Free Loading
DUST
SUPPRESSION
HOPPER
STOP DUST AT THE SOURCE
DSH Systems prevent the generation of dust, rather than attempting to remove or suppress it.
Clients around the world choose DSH for its low cost, low maintenance, and long-term solution to preventing fugitive dust.
HOW IT WORKS
REDUCE DUST BY UP TO 90%
* Dust reduction percentage is product and installation dependent
*Optional Dust Filter Covers on standard models can help reduce dust further by preventing billowing from the top of the hopper.
WHY CHOOSE A DSH?
-
DSH systems help keep product safe by protecting the integrity of blends and mixes in products such as fertiliser, as well as preventing damage to delicate items such as wood pellets. All whilst ensuring that all of your product gets loaded, to maximise capacity and profit.
-
By reducing the amount of fugitive dust in the workplace, DSH systems create a healthier, safer environment for workers. The dust suppression hopper also helps to ensure that health and safety protocols and regulations regarding the production of, and exposure to, dust is below specified levels.
-
With no internal moving parts and only needing a simple set of springs in order to function, the dust suppression hopper systems also require no electricity, hydraulics, or pneumatics, meaning there is less ongoing maintenance needed, and any servicing that is due is a simple and quick task.
-
The DSH saves manpower and time as it requires no personnel input during loading. As the DSH operates completely autonomously using its spring system, the DSH reduces the need for constant supervision and adjustments, allowing for faster loading, all whilst reducing dust.
-
DSH systems keep dust particles condensed within the material itself which prevents fugitive dust from escaping when transferring products. This means less product is lost during loading, and reduces waste, contamination, and housekeeping associated with dust.
-
The Dust suppression hopper takes care of the environment by reducing the amount of harmful dust that can escape into the air. With a DSH dust is prevented from escaping during loading or transferal, which improves both air quality and visibility on worksites as well as in surrounding areas.
SEE OUR WORK

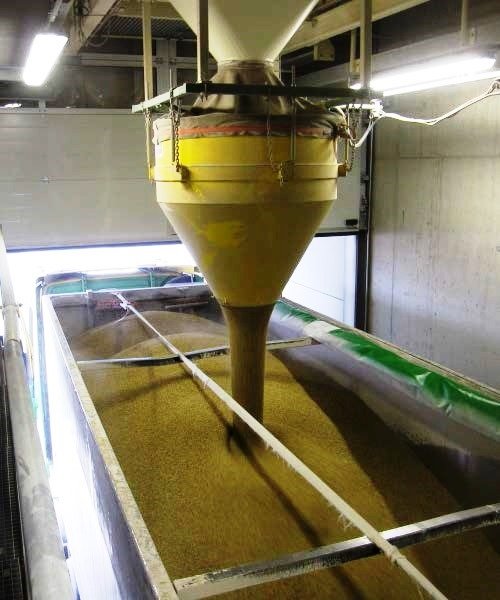
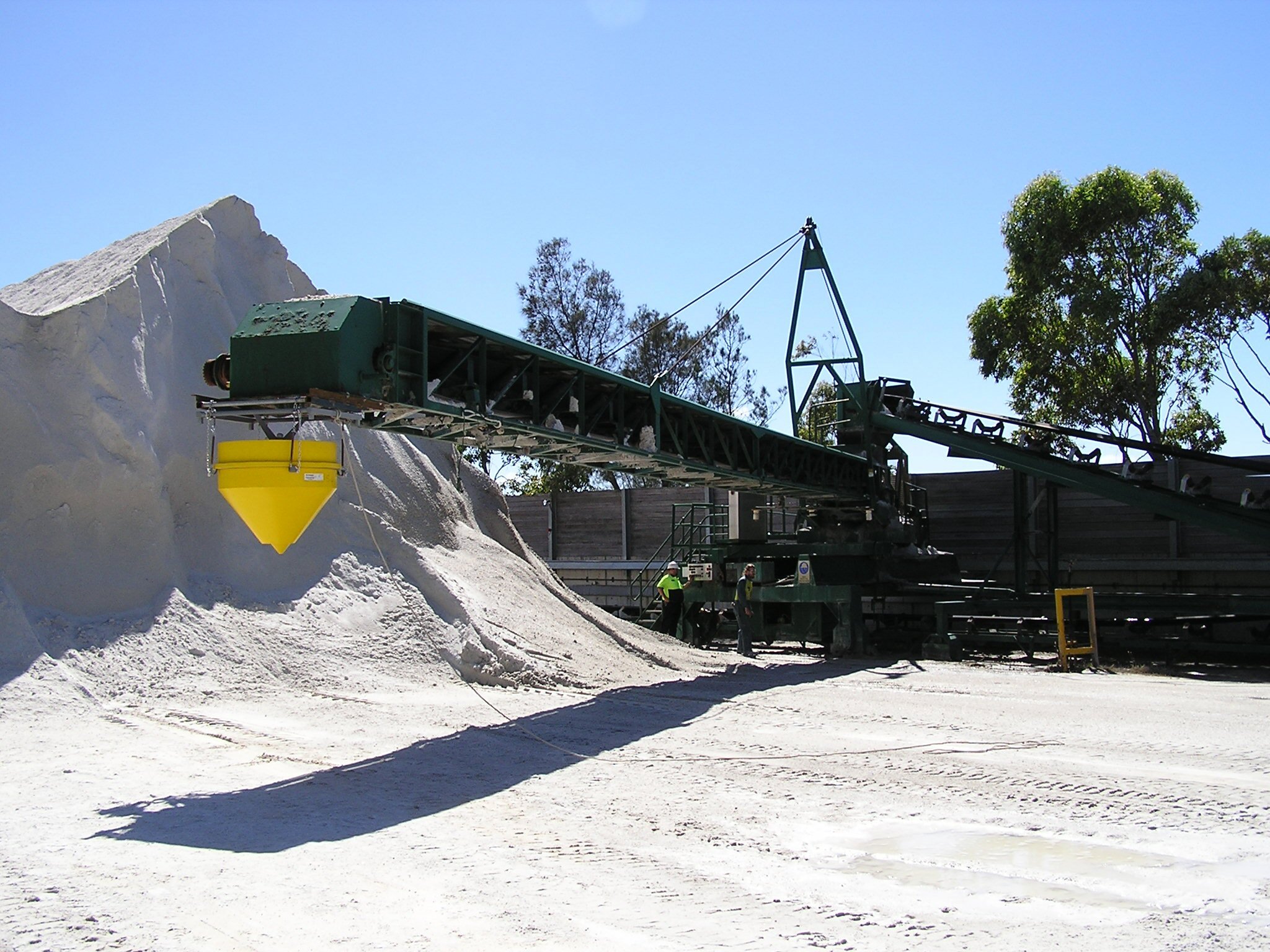
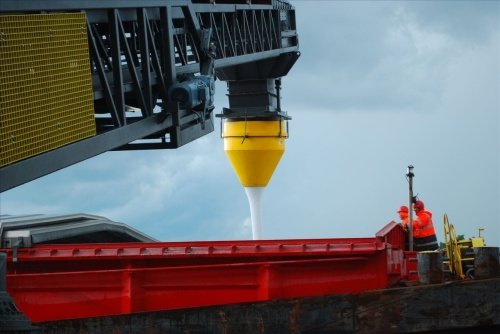

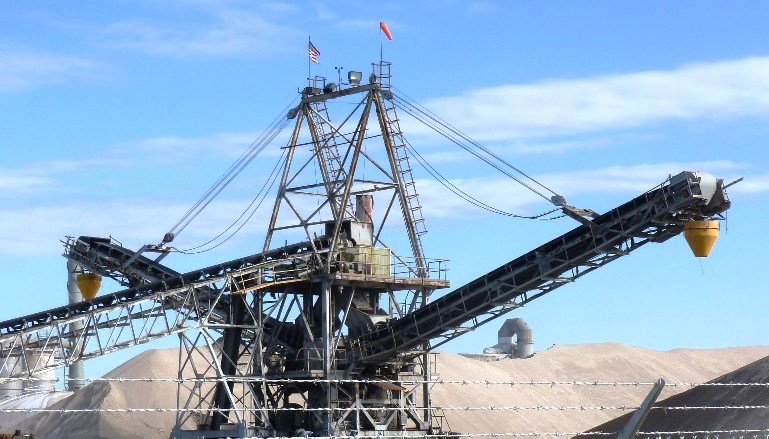

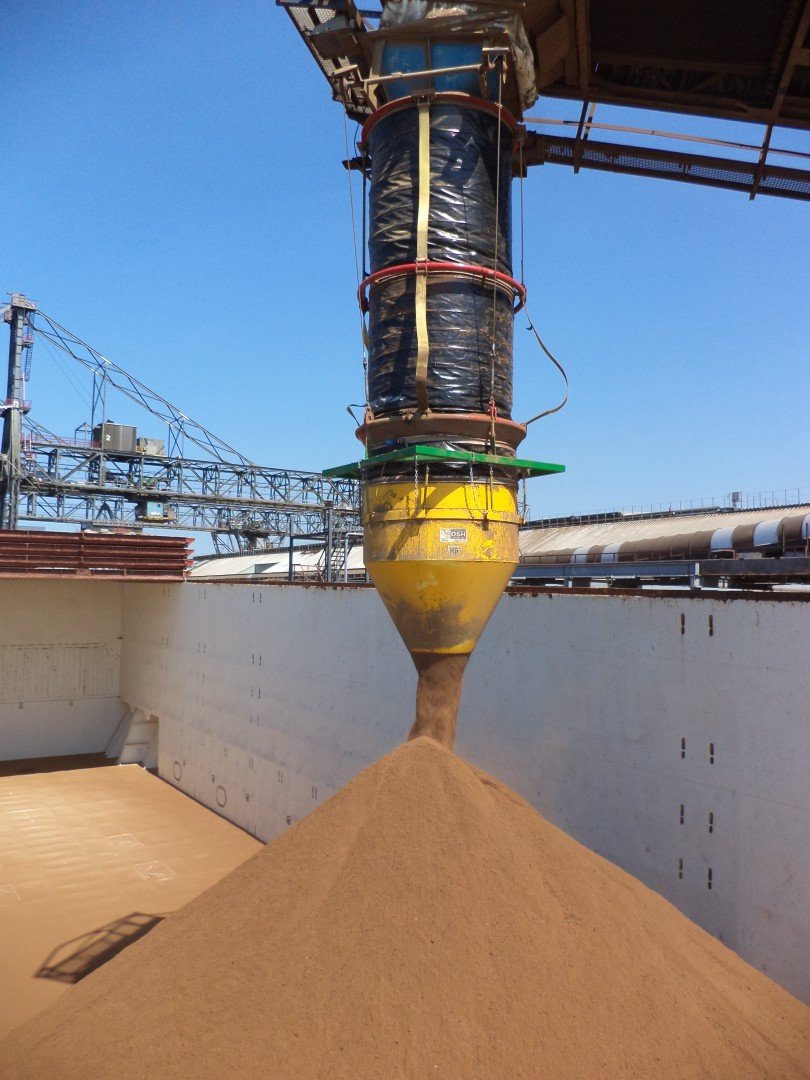
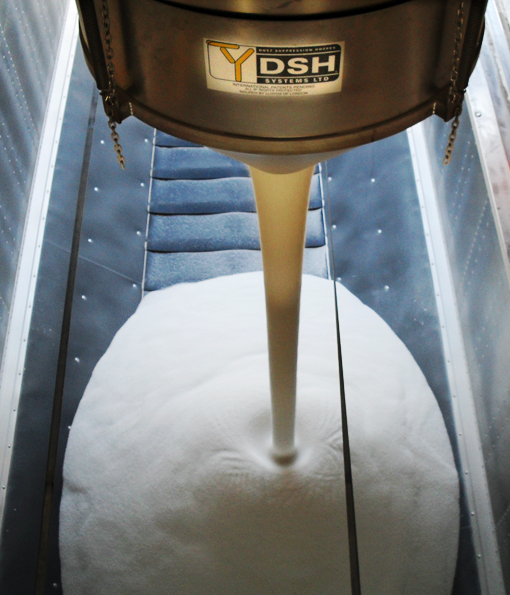
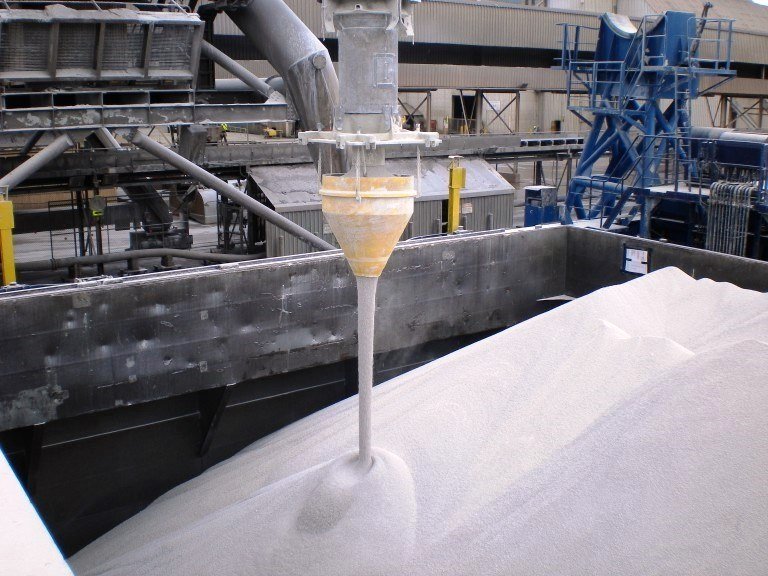
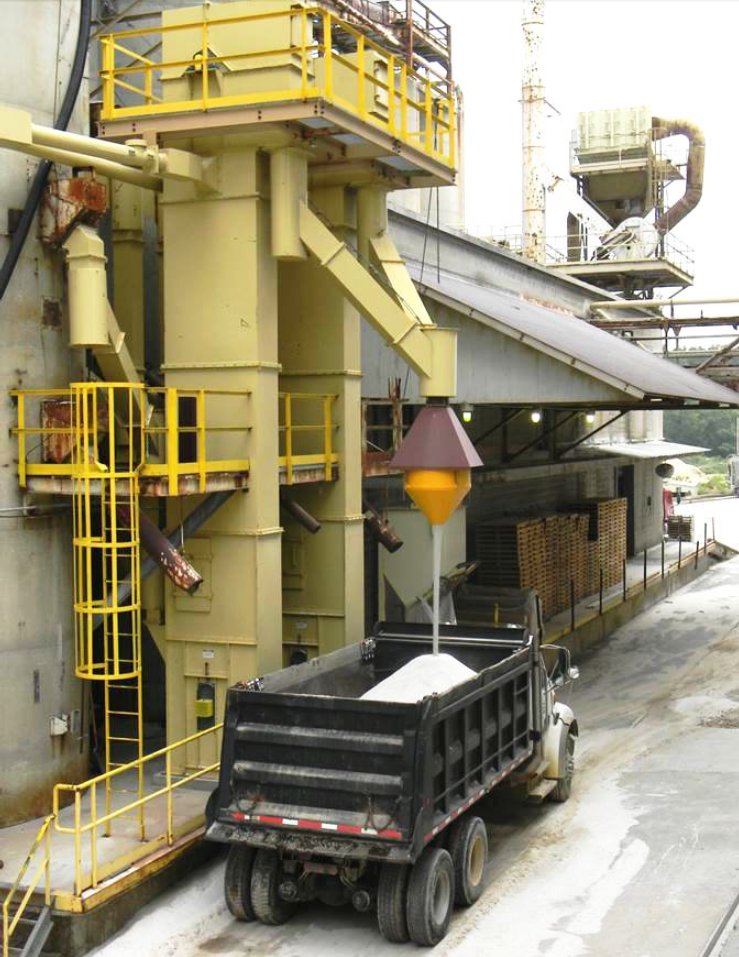
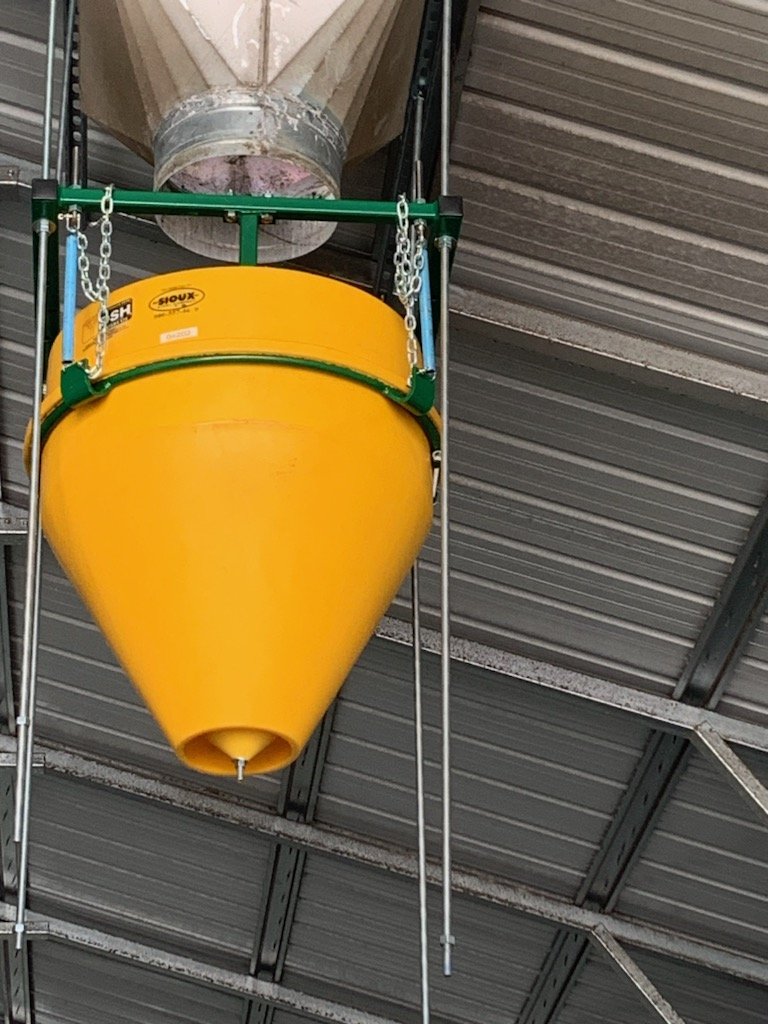
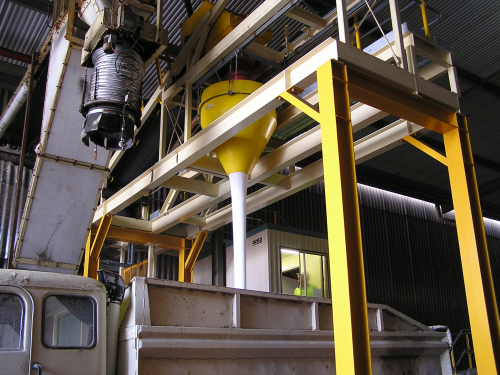
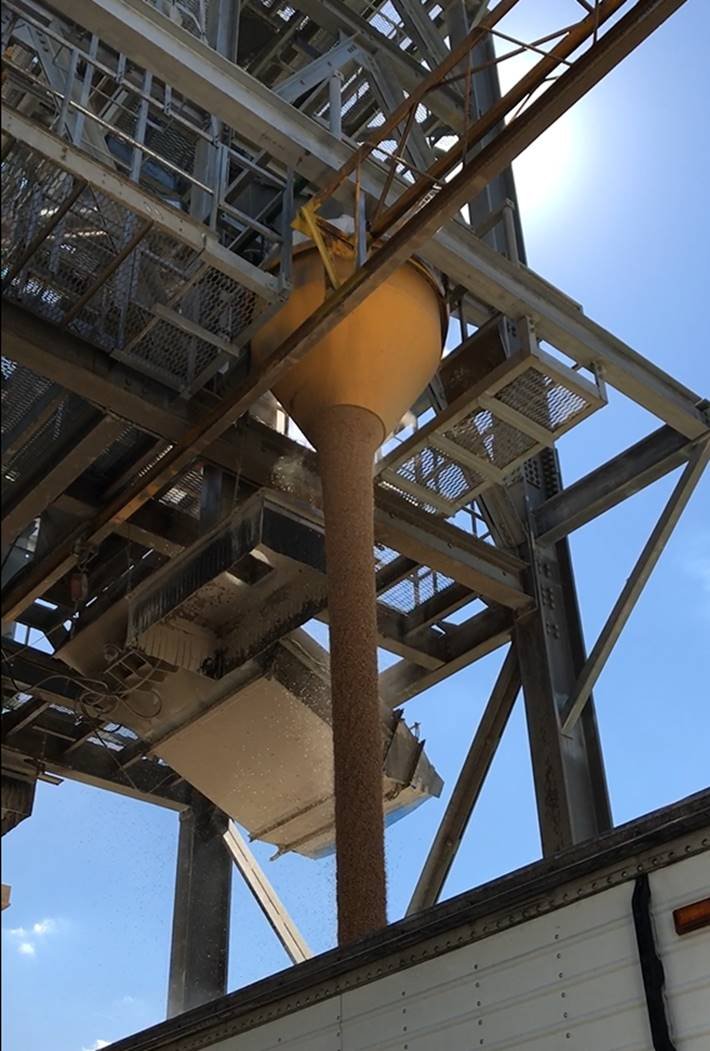
MEET THE TEAM
-
DSH Systems
DSH hopper systems are the invention of Trevor Schwass, a maintenance engineer who was asked to formulate an idea to aid in reducing dust and improve air quality at a fertiliser plant.
So, In 2004 our award winning dust suppression hopper was born - a simple, autonomous systems that required minimal utilities, maintenance or expertise to install, and the “magic bucket” has been clearing the air ever since.
Since then, DSH has installed over ten thousand hoppers across 40 countries and now has a global distribution network.
-
SIOUX STEEL COMPANY
Sioux Steel, Family owned since 1918
Sioux Steel Company manufactures grain bins, bunker walls, buildings, livestock equipment and garden beds in the heart of America! Sioux Steel has been representing DSH Systems throughout the United States for over 15 years, and during that time has installed thousands hopper systems throughout the USA!
What DSH Clients Say